V mestu Mizunami, ki je od Tokia oddaljeno nekaj ur vožnje z vlakom, stoji zaprto srednješolsko poslopje, ki japonskim proizvajalcem avtomobilov zagotavlja povsem drugačno vrsto izobraževanja. Podjetje za povratni inženiring, imenovano Caresoft Global Technologies, je staro šolo spremenilo v laboratorij za proučevanje električnih vozil. Tu razstavljajo električne avtomobile in tako analizirajo inovacije v njih, pripravljajo predloge za nižanje stroškov in te predstavljajo konkurenčnim proizvajalcem avtomobilov. Nekatere gostujoče stranke kupe sestavnih delov proučujejo v starih učilnicah, kjer se table še vedno prašijo od krede. V sobi, kjer so nekoč shranjevali žoge za odbojko, druga skupina pregleduje podatke, zbrane iz visokoenergijskih rentgenskih naprav. V nekdanji telovadnici pa se skriva nekaj, kar bi družbo Toyota Motor, vodilnega svetovnega proizvajalca avtomobilov, lahko resno skrbelo.
Po lesenem podu, prekritem s spomini na trojke in neustavljive podaje, je ekipa podjetja Caresoft namestila razstavljene trupe električnih vozil , kot sta Teslin model Y in BYD seal. Pri primerjavi njihovih delov najpomembnejšo vlogo igra zmanjševanje teže. Če želijo električna vozila v panogi še naprej loviti korak, se morajo v primerjavi z vozili na tradicionalno gorivo ukvarjati z dosegom. Zato se morajo pri skorajda vsaki odločitvi o zasnovi vprašati, ali bo avto zaradi nje kaj lažji.
Kot osnovni primer si oglejmo naslednji sestavni del, Toyotin del # 55330-42410, dobrih devet kilogramov težak jeklen drog, ki ga inženirji poznajo kot avtomobilski prečni nosilec. Volan in instrumente na armaturni plošči ta nosilec pomaga držati na svojem mestu, kabino pa hkrati ščiti med morebitnim trčenjem.Ta del je vgrajen tudi v notranjost modela bZ4X, edinega množično prodajanega povsem električnega avtomobila znamke Toyota, saj gre za preizkušeno in uveljavljeno zasnovo, ki se uporablja tudi v nešteto drugih modelih. Današnji standardni prečni nosilec je sad postopnih izboljšav, ki so nastajale skozi desetletja, večina njegovih različic pa je svoje mesto našla pod pokrovi avtomobilov z notranjim zgorevanjem. To priča o kakovosti proizvodnega sistema znamke Toyota, ki nenehno izpopolnjuje tudi najmanjše podrobnosti posameznih avtomobilskih delov. S pomočjo neskončno preizkusov je bil nosilec zasnovan tako, da preprečuje, da bi tresljaje motorja z notranjim zgorevanjem čutili tudi potniki.
Preberi še
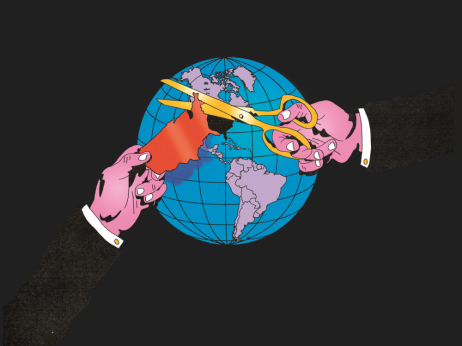
Ali je deglobalizacija sploh mogoča?
Trenutno je v modi zaščita nacionalnih interesov. Za dodatek: zgodba o robotskih taksijih naj nam bo v opozorilo.
17.03.2025
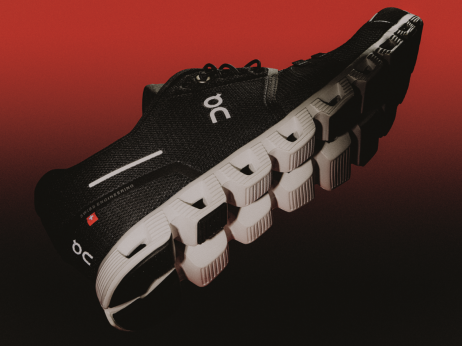
Švicarska blagovna znamka teče hitreje kot Nike in Adidas
Podjetje, ki jih izdeluje, prevladuje tudi na področju tekaške obutve in udobnih superg za vsak dan.
11.03.2025
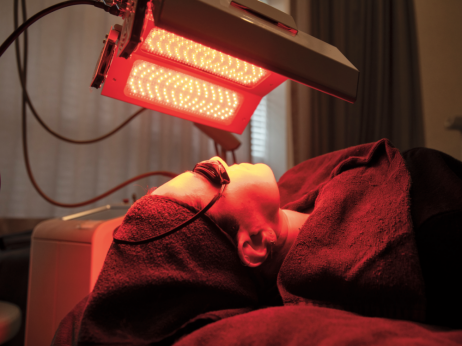
Razcvet plastične kirurgije v Južni Koreji privablja preobremenjene zdravnike
Tujci hitijo v Seul na kozmetične posege, medtem pa bolnišnice zavračajo domačine.
14.03.2025
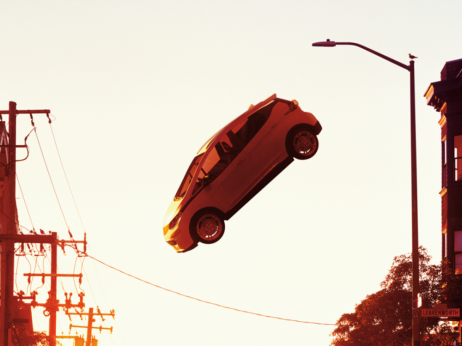
Zakaj bi morala AI vlagatelje skrbeti nesreča samovozečega avtomobila
Robotski taksiji naj bi bili lažji del avtomatizacije, toda neuspešna prizadevanja družbe GM kažejo, kako zelo je industrija oddaljena od izpolnitve svojih obljub.
07.03.2025
Elektromotorji pa se ne tresejo in jeklo je težko. Družbi Tesla in BYD, vodilna proizvajalca baterijskih električnih vozil, prav iz teh razlogov podobne nosilce izdelujeta iz plastike. Takšni nosilci po podatkih podjetja Caresoft tehtajo le dobrih šest kilogramov, poleg tega pa so tudi cenejši in lažji za vgradnjo.
Shiho Fukada za Bloomberg Businessweek
Ta sprememba se na prvi pogled zdi zelo preprosta; če se še nikoli niste ukvarjali z bencinskim motorjem, pa tudi intuitivna. Če ste vse življenje razmišljali le o mikroizboljšavah – ki zadevajo samo jedro kaizena, filozofije, ki podpira Toyotin proizvodni sistem ali TPS – boste imeli s tovrstnimi zamislimi težave. "Za premik od vozila z notranjim zgorevanjem do električnega vozila potrebujete kaj več kot le kaizen," pravi Terry Woychowski, predsednik podjetja Caresoft in nekdanji izvršni direktor General Motors. "Prav to je dilema družbe Toyota."
Zunaj področja električnih vozil podjetju Toyota ne gre samo dobro, marveč odlično. Pri prehajanju proizvodnih linij k povsem električnim modelom je sicer zaostajalo celo za konkurenti stare šole, a v preteklem letu se je to izkazalo za pametno potezo. Povpraševanje po električnih avtomobilih je resda raslo, vendar ne tako hitro, kot si je obetala tri bilijone dolarjev vredna avtomobilska industrija, ki je v razvoj vložila na milijarde dolarjev. Nabor izdelkov Toyota je obsegal približno dve tretjini vozil z notranjim zgorevanjem, tretjino hibridnih in 0,1 odstotka električnih vozil, in zadeva se jim je odlično izšla. Podjetje je še povečalo svojo prednost pred dolgoletni tekmeci (Volkswagen, Hyundai, GM) in ocene kažejo, da je leta 2024 prodalo več kot 11 milijonov vozil v primerjavi s podjetjem Tesla, ki je prodalo 1,8 milijona primerkov, in podjetjem BYD, ki jih je prodalo 4,3 milijona (od tega 1,8 milijona električnih). Predsednik Akio Toyoda je vztrajal pri "razvejeni strategiji", kar je v praksi pomenilo hibride, tradicionalno gnana vozila in celo avtomobile na vodikov pogon. Čeprav je Toyoa, ki je star 68 let, leta 2023 vlogo izvršnega direktorja prepustil Kojiju Satu, nekdanjemu direktorju družbe Lexus, ima kot predsednik še vedno zadnjo besedo.
"Toyotinih 11 milijonov prodanih primerkov je skupna vsota kupcev v različnih državah in številnih modelov," pravi Tatsuo Yoshida, analitik pri Bloombergu Intelligence. "Ohranjanje tako visoke ravni proizvodnje nikakor ni preprosto. Številni drugi proizvajalci avtomobilov le stežka presežejo šest milijonov." Podjetje izgube ni zabeležilo že od leta 2009 (tik preden je predsednik postal Toyoda) in od takrat je uspešno prestalo že vrsto spodrsljajev.
Dolgoročno pa bi lahko Toyodov odpor do korenitega premisleka o družinskem podjetju oviralo sposobnost podjetja pri snovanju avtomobilov prihodnosti. TPS je družbo Toyota – in njene brezsramne posnemovalce po vsem svetu – privedel do tega, da se je oborožila s specializiranimi inženirji, se osredotočila na racionalizacijo montažnih procesov in izdelavo čim več komponent prepustila zunanjim dobaviteljem. Te poteze so družbi pomagale povečati učinkovitost zrelega, komoditiziranega trga strojne opreme. Za strojno opremo, ki si svojo pot šele utira, so takšne poteze pogosto obremenilne.
Podjetji Tesla in BYD sta poskrbeli, da so njuni proizvodni obrati cenejši in bolj modularni, medtem ko si prizadevata za samostojno proizvodnjo večjega števila delov. Razlog za to je deloma dejstvo, da oblikujejo nove dele ali njihove kombinacije, ki jih na policah dobaviteljev ni mogoče dobiti. (Tipično električno vozilo po oceni skupine Goldman Sachs Group sestavlja približno 11tisoč delov, kar je približno dve tretjini manj kot njegov ekvivalent na fosilno gorivo.) V igri je tudi prizadevanje, da bi večji del tehnologije ohranili pod svojim intelektualnim lastništvom, to pa je nekaj, s čimer se direktorjem v avtomobilski industriji v preteklosti že več generacij skorajda ni bilo treba ukvarjati. Nagib k izdelkom po meri pa pomeni, da bodo poznejši uporabniki (tudi tisti premožnejši) težje samo kopirali in izboljševali tisto, kar so si izmislili njihovi predhodniki. "Če ne sprejmemo novega načina razmišljanja, bomo vedno v zaostanku," pravi Shinichi Sasaki, nekdanji izvršni podpredsednik v podjetju Toyota, ki zdaj vodi Zvezo japonskih znanstvenikov in inženirjev.
Toyota
Na naša vprašanja so se v družbi Toyota odzvali z izjavo, da proizvodna filozofija družbe obsega veliko več od zgolj oblikovanja delov in proizvodnih korakov ter da uteleša pripravljenost na učenje iz napak in morebitnih izgub. "Na izboljšave gledamo kot na priložnosti za razvoj," je v izjavi dejal Aki Irie, generalni direktor za javne zadeve. "TPS je način razmišljanja, ne le metoda za izboljšanje učinkovitosti."
Na vsakoletnem tehnološkem sejmu CES v Las Vegasu je Hiroki Nakajima, glavni tehnološki direktor podjetja, za Bloomberg Businessweek povedal, da je njegovo podjetje pod pritiskom, vendar je odločeno, da ta pritisk tudi premaga. "V tem trenutku so velika grožnja naši kitajski konkurenti, vendar pa želimo svojo tehnologijo toliko izboljšati, da te konkurente premagamo," je dejal. "80 odstotkov tehnologije je povsem preprosto zamenjati, najpomembnejših pa je preostalih 20 odstotkov."
V nekdanji telovadnici srednje šole v Mizunamiju se zdi povsem jasno, da bo električna prihodnost zahtevala nekaj sprememb, ki so pod omejitvami kaizena in TPS nepredstavljive. V podjetju Tesla so sedeže svojih vozil pritrdili neposredno na baterijo, ki opravlja dvojno funkcijo kot strukturni sestavni del vozila. Druga podjetja baterijo na polnilni vhod pritrdijo z debelo bakreno žico in pritrdilnimi elementi, podjetje Tesla pa je čas vgradnje skrajšalo z uporabo toge aluminijaste cevi. Podjetje BYD je izdelalo sestavni del #KTZ55X55S-A, ki nekdanjo osmerico sestavnih delov električnega pogonskega sklopa združuje v en sam modul. Ta vključuje integrirano strojno in programsko opremo za funkcije, kot sta upravljanje baterije in inverzija električne energije (pretvorba enosmernega toka v izmenični tok).
Kombinirani sistem tehta in stane približno 20 odstotkov manj od posameznih sestavnih delov, navaja raziskovalna skupina Yole Group, ki ugotavlja, da družba BYD 40 odstotkov svojih delov proizvaja sama. "In človek ob tem pomisli – madona, ti fantje naredijo prav vse," pravi Woychowski, predsednik podjetja Caresoft. "Izdelujejo svoje baterije. Izdelujejo svoje motorje. Izdelujejo svoje karoserije. Izdelujejo sprednje in zadnje maske, žaromete, obloge vrat, konzolo. To je kvantni skok. Za kaizen to ne pomeni nič dobrega."
Znamka Toyota se je rodila s povsem drugačnim proizvodnim skokom. Pred stoletjem je Sakichi Toyoda, Akiov pradedek, izumil avtomatizirane statve, ki so si lahko samodejno podajale več niti in v nastali tkanini zaznale tudi luknje, pri čemer so se samodejno zaustavile, dokler delavec v bližini ni odpravil težave. Ko je Sakichi ustanovil svoje podjetje, je njegovo tkalnico v središču mesta Nagoya poganjal premog. Do poznih 30. let prejšnjega stoletja so že vse statve delovale s pomočjo električnih motorjev (zaradi česar so bile učinkovitejše, enostavnejša pa so bila tudi popravila), Sakichijev sin Kiichiro pa je svoje izkušnje s proizvodnimi linijami uporabil pri ustanovitvi avtomobilskega podjetja. Do konca 50. let se je predmestje mesta Nagoya, ki si ga je družba Toyota izbrala za svoj sedež, preimenovalo v Toyota City, sledila pa je prevlada na svetovnem trgu.
Skozi desetletja se je celotna panoga preoblikovala v skladu s smernicami, ki jih je zarisala prav družina Toyoda, te pa so narekovale čim bolj prečiščene proizvodne linije, hkrati pa mrzlično osredotočenost na zniževanje stroškov. Bili so časi, na primer, ko so proizvajalci avtomobilov zaposlovali cele vojske delavcev, ki so popravljali napake na avtomobilih, ki so prišli z montažne linije. Tega večinoma ne počnejo več. Družba Toyota je posvojila idejo o odpravljanju težav v istem trenutku, ko jih delavci opazijo, namesto da bi čakali, da bo avtomobil do konca izdelan.
Kazhiro Nogi/AFP/Getty Images
Številni standardi družbe Toyota se do danes ohranjajo kot standardi celotne industrije. Med nedavnim obiskom tovarne tovornjakov F-150 družbe Ford Motor v michiganskem Dearbornu je na montažni liniji mrgolelo Toyotinih nadzornih zaslonov, v bližini pa je stala tabla za odpravljanje težav z oznako kaizen. Ko gre za visokokakovostno masovno proizvodnjo, Kumar Galhotra, glavni operativni direktor družbe Ford, pravi takole: »Cilj je zelo hiter napredek, da ujamemo korak s podjetjem Toyota.« Na domačih tleh je družba Toyota vredna več kot naslednja tri največja podjetja na tokijski borzi.
Leta 2010 – leto po tem, ko je vodenje prevzel Akio – je družba Toyota za 50 milijonov dolarjev kupila triodstotni delež v družbi Tesla. Zadnji preostanek tega deleža je v letu 2016 za dober dobiček prodala, saj se je želela osredotočiti na izdelavo lastnih električnih vozil. Skoraj desetletje pozneje pa je vrednost družbe Tesla dramatično višja (tržna kapitalizacija: približno 1,3 bilijona dolarjev), družba Toyota pa se na področju električnih vozil zmore pohvaliti le s tremi tovarnami, v katerih še vedno večinoma izdelujejo druge vrste avtomobilov.
To je inženirje v podjetju Toyota prisililo k uvedbi določenih rešitev, ki kršijo zapovedi filozofije kaizen, vendar so nujne za izvedbo številnih postopkov, ki so pri izdelavi električnih vozil precej drugačni ter bi morali zahtevati veliko manj prostora in manj ljudi. Številne okvirje karoserije bZ4X je treba umakniti z glavne montažne linije, vanje vgraditi baterije in jih nato ponovno namestiti na glavno linijo, to pa zahteva dodaten prostor in čas. »Ali bo to najučinkovitejša proizvodna linija? Verjetno ne,« pravi Susan Elkington, najvišja izvršna direktorica za proizvodnjo električnih vozil Toyota v ZDA. »A proizvodnega traku ne morete kar tako iztrgati iz tal in ga čez noč prestaviti nekam drugam. V obdobju spreminjajoče se tehnologije je prilagodljivost pri tem prehodu ključnega pomena.«
Dokler se Toyota ne zaveže gradnji objektov, prilagojenih posebej za nove modele, se bodo njeni strokovnjaki za avtomatizacijo pri razvoju procesov za električna vozila verjetno soočali s številnimi težavami. Mike Cicco, operativni vodja za ZDA v družbi Fanuc Corp., kraljici industrijske robotike, pravi, da je v starejših obratih težje uvesti nove proizvodne postopke, zaradi česar so podjetja »nekako omejena v smislu Tale linija je tukaj, tale linija pa je tam«. Do težav je v podjetju Toyota prihajalo tudi na oddelkih za oblikovanje in inženiring. Leta 2022, leto po tem, ko je predstavilo svoj električni model bZ4X, so jih morali na tisoče odpoklicati, ker so se vijaki, s katerimi so bila pritrjena kolesa, nenehno rahljali. Razvijalci niso povsem razumeli, koliko navora bodo ustvarjali elektromotorji avtomobilov, in so uporabili vijake, ki obremenitve niso zmogli prenesti.
Shiho Fukada za Bloomberg Businessweek
To je bil neprijeten opomnik, da se v perfekcionizem usmerjena filozofija družbe Toyota ni vedno prenesla na njene avtomobile. Množični, večmilijonski varnostni odpoklici avtomobilov so zaznamovali uvodni del mandata Akia Toyode, ameriška vlada pa je leta 2010 navedla, da naj bi okvarjena vozila Toyota prispevala k smrti skoraj stotih Američanov. Leta pozneje je podjetje priznalo, da je svoje stranke in regulatorje zavajalo, in v sporazumu za odložen pregon privolilo v plačilo takrat rekordnih 1,2 milijarde dolarjev.
Junija lani pa je japonsko ministrstvo za promet družbi Toyota (skupaj s podjetji Honda in Mazda) izdalo opomin zaradi ponarejanja in prirejanja podatkov o varnosti vozil med postopkom prijave za vladne certifikacije. Za nameček je ista dejanja priznala tudi vrsta Toyotinih hčerinskih družb in podružnic, kar je sprožilo zaustavitev proizvodnje, medtem ko so inženirji izvajali predpisane korake za namene certificiranja. Na tiskovni konferenci se je predsednik Toyoda v znak opravičila priklonil, kar je prvi in obvezni korak, ki se zahteva od japonskega direktorja podjetja, zasačenega v škandalu. A že pri prvem vprašanju je bilo z opravičili konec.
Ko je novinar vprašal, ali ta polom pomeni, da je proizvodna filozofija družbe Toyota dosegla svoje meje, ga je Toyoda premeril s hladnim pogledom in odgovoril: "To nikakor ne drži." Njegova ekipa se je močno trudila, je dejal, da bi načela filozofije kaizen uporabljala za reševanje kakršnihkoli težav, tako kot vedno.
Toyoda je svojo strategijo različnih pristopov odločno zagovarjal kot funkcijo zadovoljevanja povpraševanja strank, vendar pa se v njej skriva tudi osebna nota. Poleg družinske zapuščine že vse življenje obožuje tudi dirkalne avtomobile in, kot je pred nekaj leti dejal na avtomobilskem salonu v Tokiu, »vonj po bencinu in veliko hrumenja«. Zaradi njegove predanosti proizvodnji avtomobilov stare šole mora Sato, novi izvršni direktor podjetja in izkušeni Toyotin inženir, zdaj ugotoviti, kako bo poskrbel za prihodnost podjetja, ne da bi pri tem pretirano posegal v njegovo sedanjost.
"Imenovanje Sata je bilo pametno in nakazuje na priznavanje potrebe po prehodu v naslednjo generacijo," pravi Jeffrey Liker, profesor industrijskega inženiringa na Univerzi v Michiganu in avtor knjige The Toyota Way. "Sato je mlajši posameznik, nadvse bister inženir, ki se je v preteklosti proslavil z doseganjem ciljev, ki so se zdeli nemogoči." Liker je Satu priznal ključno vlogo pri razvoju prvih hibridov znamke Toyota, v zadnjem času pa tudi športnega kupeja LC znamke Lexus.
Ko je leta 2023 prevzel položaj izvršnega direktorja, je Sato obljubil, da bo Toyota leta 2026 prodala 1,5 milijona električnih avtomobilov. Na tej točki se to sliši bolj kot pravljica. Če bi vsake toliko časa malce pokukali v Toyotine obrate, pa bi lahko opazili zametke oprijemljivega načrta. Leta 2023 so na dnevu odprtih vrat inženirji v raziskovalnem centru podjetja v bližini gore Fuji na ogled postavili polprevodniške baterije daljšega dosega, modele samovozečih sistemov in eksperimentalni električni avtomobil, ki je (morda določenemu šefu na ljubo) zasnovan tako, da tako po videzu kot po zvoku spominja na močan športni avto – kolikor seveda to dopušča zasnova škatlaste limuzine. Poleg sklopke je v tem vozilu tudi stopalka za plin, ta pa je povezana z zvočnikom, ki ob menjavi prestave predvaja zvoke hrumenja motorja. Vse skupaj vzbuja rahel vtis "sfriziranega" avtomobila, ki pa ga je bilo kljub njegovi prismojenosti prav zabavno voziti. Sato od takrat tiho nadzoruje milijarde dolarjev porabe za proizvodnjo baterij in nadgradnjo treh Toyotinih tovarn, ki so deloma usmerjene v izdelavo električnih vozil – ene na Japonskem in dveh v ZDA. (Družba Toyota se dogovarja o gradnji nove tovarne za proizvodnjo elektrificiranih modelov znamke Lexus na Kitajskem, poroča Bloomberg News.)
Motomachi, japonska tovarna za proizvodnjo električnih vozil, stoji približno 10 minut vožnje od sedeža družbe Toyota. Med našim obiskom lansko poletje smo imeli možnost videti sivi model bZ4X, kako drsi po montažni liniji, medtem pa so zaposleni vanj namestili sedeže, ožičenje in komponente pogonskega sklopa. Dvema delavcema je skoraj 500-kilogramsko baterijo uspelo v avto namestiti v gladko povezani seriji gibov, ki je trajala nekaj več kot 90 sekund. Deli so v zabojnike in nato na stojala romali z vzporednih postaj, digitalni zasloni nad glavami delavcev pa so prikazovali stanje vsakega koraka v postopku montaže. Ko je bil bZ4X pripravljen za nadaljnje korake, se je linija vrnila v način običajnega delovanja in se lotila sestavljanja bele hibridne limuzine Crown in nato vozila Noah, enoprostorca na bencinski pogon.
Tomohiro Ohsumi/Getty Images
Vsakdo iz podjetja Toyota vam bo zatrdil, da izdelava več vozil na isti montažni liniji ponazarja načela TPS, to pa podjetju omogoča prilagodljivost pri izdelavi različnih modelov kot odziv na spreminjajoče se zahteve trga. "S prehajanjem med različnimi vrstami vozil brez hrambe zalog je uravnotežena in izravnana tudi delovna obremenitev dobaviteljev," je v izjavi podjetja dejal Irie.
Pri pripravah na prihodnost pa nima težav zgolj Toyota. Družba GM, vodilna med tremi velikimi proizvajalci avtomobilov v Detroitu, je preklicala svojo obljubo, da bo do leta 2035 prešla na izključno proizvodnjo električnih vozil. Družba Ford, ki je ustanovila ločen oddelek za električna vozila, je določene dele svoje strategije o električnih vozilih začasno dala na čakanje. Družba Volkswagen kar pet milijard dolarjev vlaga v zagonsko podjetje Rivian Automotive z električnimi vozili, naložba pa se do danes še zdaleč ni izplačala. Podjetje Rivian za vsako vozilo, ki ga proda, v povprečju izgubi 39 tisoč dolarjev.
Toyota pa ima, vsaj kar zadeva časovno vodstvo na področju električnih vozil, vendarle nekakšnega asa v rokavu. Imenuje se Prius. Tisti, ki so otroštvo preživeli na njegovi zadnji klopi, se še megleno spomnijo, kako radikalno je bilo v poznih 90. letih bencinski motor kombinirati z električnim motorjem, da ste z avtomobilom za množični trg tako dosegli porabo 4.7 l/100 km. Zapletenost sistema je podvojila stroške izdelave pogonskega sklopa v primerjavi s konvencionalnimi modeli, na račun tega pa je podjetje Toyota več let vsako svoje hibridno vozilo prodalo z izgubo. Ta poteza je bila v marsičem v očitnem nasprotju s TPS. A Hiroshi Okuda, ki je bil v družbi Toyota približno desetletje predsednik in nato, začenši sredi devetdesetih, tudi predsednik uprave, je stremel k temu, da se je denar porabil za diverzifikacijo tehnologije in ponudbe podjetja.
Ime Okuda se v uradni zgodovini podjetja od takrat ne pojavlja več pogosto. Ko je nasprotoval ponovnemu prevzemu nadzora družine Toyoda, je s tem prelomil načelo solidarnosti. "Japonska avtomobilska industrija je zmogla v panogi prevzeti vodstvo v svetovnem merilu, zdaj pa je v položaju, ko mora to vodstvo ubraniti," pravi Hiroto Saikawa, nekdanji izvršni direktor družbe Nissan. "Pri temeljitem premisleku o stvareh in učenju iz njih se država ni najbolje odrezala. A nobena druga država nima tako številnega nabora inženirjev tako visoke kakovosti. Če se bodo voljni učiti, bodo lahko še vedno dosegali lepe uspehe."
Tisti člani družine Toyoda, ki odločitve sprejemajo dandanes, bodo morali razmišljati pogumno. Daisuke, Akiov sin, je višji podpredsednik v hčerinski družbi, ki se ukvarja s tehnologijo samovozečih vozil in drugimi dolgoročnimi načrti. A Toyota ima trenutno druge načrte. Podjetje je v začetku tega leta napovedalo, da se loteva povsem novega razreda motorjev z notranjim zgorevanjem, ki bodo nekega dne lahko delovali na različne vrste tekočega goriva, vključno s čistejšimi različicami, kot je vodik. V družbi Toyota pravijo, da bodo motorji zaradi manjših dimenzij in večje moči kot nalašč za hibride naslednje generacije.
"Zavedamo se, da bodo kritiki pomislili: Zakaj prav zdaj?" je spomladi na vzdržljivostni dirki v slogu Le Mansa na dirkališču Fuji Speedway dejal Nakajima, odgovorni uslužbenec za tehnologijo. "Vsi vemo, da je prihodnost v električnih vozilih. A dokler se tej prihodnosti ne približamo, se bomo še naprej trudili, da bomo še boljši v tem, kar znamo najbolje."
– v sodelovanju s Tsuyoshijem Inajimo in Nicholasom Takahashijem
Trenutno ni komentarjev za novico. Bodi prvi, ki bo komentiral ...