BMW že v imenu poudarja, da gre za bavarsko tovarno motorjev. Morda malce nenavadno, toda ali ste vedeli, da BMW že leto in pol v Nemčiji ne proizvaja motorjev na notranje zgorevanje? Nemčije seveda niso zapustili, tam še vedno proizvajajo elektromotorje, sestavne dele in druge komponente. Eno najpomembnejših proizvodenj smo obiskali v začetku leta.
Bavarci v germanskem slogu ničesar ne prepuščajo naključju. Namesto da bi se do 200 metrov oddaljene sosednje stavbe sprehodili, so nas prepeljali v BMW-jevih električnih sedmicah. Čeprav je bila vožnja dolga le tri minute, sem jo izkoristil za masažo hrbta in zadnjice. Na prvi pogled tovarna ne izdaja, da gre za eno najnaprednejših livarn.
BMW
Nič ni prepuščeno naključju
Ogled smo začeli, čakajoč na tovorno dvigalo. V Landshutu - slabo uro vožnje severno od Münchna - je bil sončen, vendar mrzel dan. V počasnem tovornem dvigalu sem že kar malce nestrpno čakal, da se ogled začne, da mi ne bo treba prej še na stranišče. V dobro razsvetljenih prostorih, visokih tri nadstropja, in napolnjenih s stroji in cevmi, za katere se mi ni niti sanjalo, kakšno funkcijo imajo, nas je pričakal gospod Karl Bauer, vodja proizvodnje injekcijskega ulivanja.
Preberi še
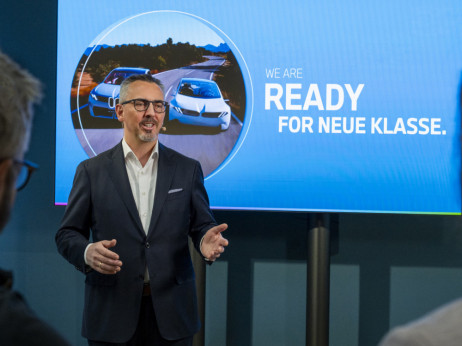
Joachim Post, BMW: Prepovedati eno tehnologijo je nevarno
Postavite stroge cilje izpustov CO2 ter nam, industriji, in kupcem prepustite odločitev, ko neka tehnologija ni več zanimiva, meni član uprave.
28.02.2025
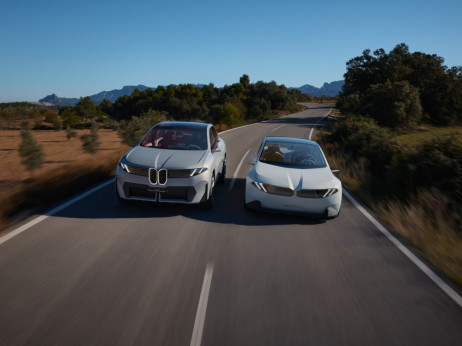
Tango Bavarcev med sanjami Bruslja in željami kupcev
BMW nam je razkril svoje prelomne novosti - električnih avtomobilov Neue Klasse.
21.02.2025
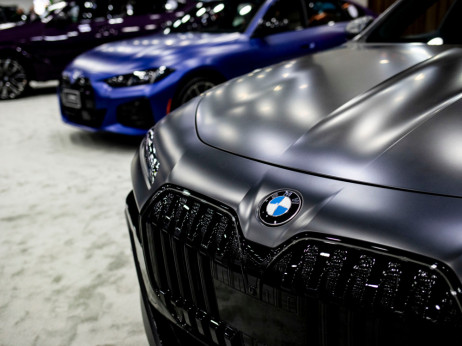
Kako močno bo zaostrovanje trgovinske vojne udarilo BMW
Izvršni direktor BMW Oliver Zipse ocenjuje, da bi jih trgovinska vojna letos lahko stala milijardo evrov
14.03.2025
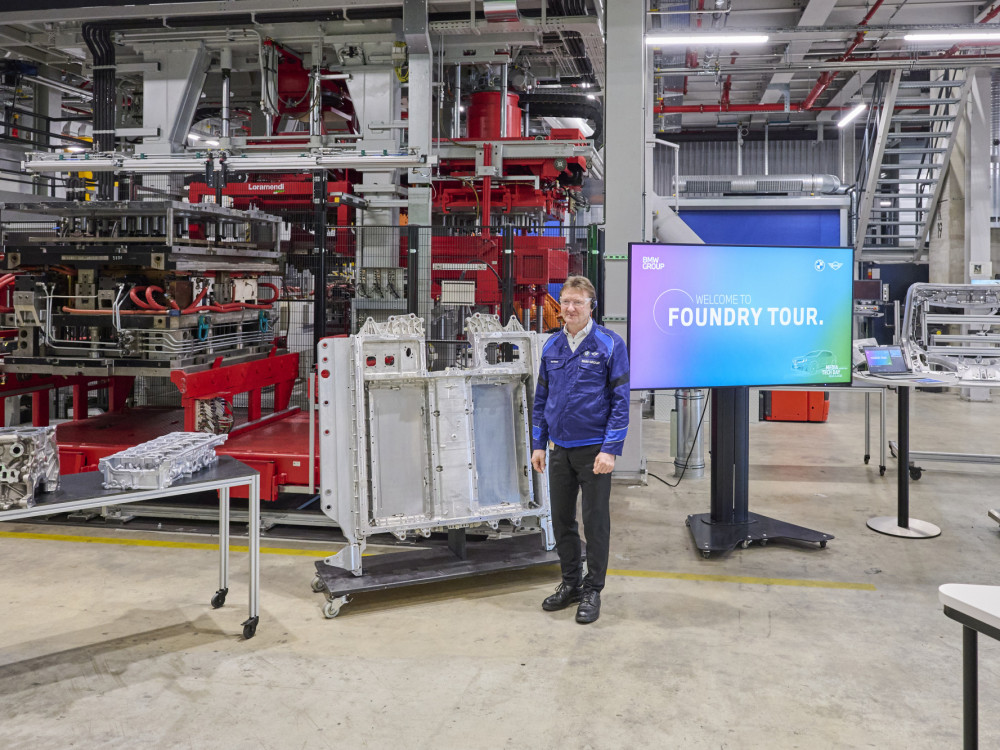
V nasprotju s temačno in ledeno garažo je bilo v livarni prijetno toplo, topleje kot doma. V roke so mi potisnili slušalke in zaščitna očala. Puhovka me je le še ovirala. Celotno tovarno segreva toplota talilnice. V Landshutu imajo posebno hibridno peč, kjer na uro stalijo približno tri tone aluminija, na dan pa od 50 do 60 ton. Aluminij namreč segrevajo do približno 800 stopinj.
Na naslednji točki začnejo proizvodnjo različnih komponent. Proizvajajo glave in ohišja motorjev, večje strukturne komponente za karoserije vozil ter komponente za električne pogone. Ogledali smo si ulivanje aluminijastega ohišja elektromotorja. Sam ulitek ohišja niti ni revolucionaren, bolj zanimivi so proizvodnji procesi. Uporabljajo pet različnih metod ulitkov. Metodo izberejo glede na komponento, tehnološke zahteve in proizvodno število.
Tom Kirkpatrick
Poseben način vbrizgavanja aluminija
Vrhunec in ključni del proizvodnje je vlivanje s pomočjo vbrizgalnikov (ICA), ki so ga patentirali v Landshutu. S pomočjo keramičnih tub na robotu vlivajo tekoči aluminij v kalup z jedri. Vbrizgalniki se premikajo in linearno vbrizgavajo vroč aluminij v šablone. Linearno vbrizgavanje je ključno pri procesu strjevanja in ohlajanja, ker skrajša čas cikla, je pojasnil Bauer. Ker vbrizgalnik vedno brizga od zgoraj, lahko vlivanje pri nižji temperaturi v zgornjem delu vodi do nadaljnjih prihrankov energije in krajših časov strjevanja, dodaja. Po Bauerjevih besedah hitrejše strjevanje prinaša višjo kakovost strukture in boljše mehanske lastnosti.
Tom Kirkpatrick
Sam postopek smo si ogledali z razdalje nekaj metrov. Prostor med stroji in roboti ter nami so ločevala dvižna plastična vrata, ki so se spustila v času ulivanja. Prvi robot v kalup postavi jedra in se umakne. Drugi se postavi nad kalup z jedri in vbrizga aluminij. Na zaslonih se izpisujejo število delov ter morebitne težave. Ko je proces končan, prvi robot ohišje elektromotorja skupaj z jedri premakne na naslednjo postajo.
Tom Kirkpatrick
Prihranki pri energiji, času in materialu
Injektorsko ulivanje zagotavlja bolj kakovostno in tanjšo mikrostrukturo ter s tem izboljšane mehanske lastnosti ulitkov. Cikel vlivanja je krajši, bistveno nižja je poraba energije in zaradi nižje temperature ulivanja tudi nižji izpusti. Temperature ne razkrivajo. Postopek zahteva manj recikliranega materiala. Vbrizgavanje s pomočjo vbrizgalnika odpravlja potrebo po dodatnem sistemu cevi, kar se odrazi v do 40 odstotkov nižji porabi taline (staljen aluminij).
Tom Kirkpatrick
Poseben ni le postopek vlivanja, temveč tudi jedra, ki jih uporabljajo. Od konca leta 2024 za vlivanje delov uporabljajo oblikovana peščena jedra oziroma šablone. Izdelujejo jih 3D-tiskalniki, ki tiskajo plast za plastjo peska. Peščena jedra izdelajo z uporabo okolju prijaznih anorganskih veziv oziroma lepil. Gre za prva takšna jedra na svetu in trajnostno metodo, zaradi katere pri vlivanju tako rekoč ne nastajajo izpusti. ''Vezivo v stiku z vročim aluminijem zgori in se spremeni v dim,'' je pojasnil Bauer. Tudi to inovacijo so razvili v Landshutu.
Tom Kirkpatrick
Rentgen brez čakalnih vrst
Ker pri jedrih uporabljajo pesek, so bila tla v delu proizvodnje, ki smo si ga ogledali, spolzka. Jedra niti niso lahka. Okroglega sem z eno roko zmogel dvigniti. Po ohlajanju ulitkov sledijo označevanje in žaganje ter predobdelava. Na teh odstranijo viške strjenega aluminija, ki se ga vrne na začetek proizvodnje - v peč. Ohišje elektromotorja se pomakne na naslednjo postajo, kjer ga čakajo peskanje, mehanska obdelava ter čiščenje. Sledi še en zanimiv korak v proizvodnji. Stroj na vsakem ulitku opravi računalniško rentgensko diagnostiko. Čakalnih dob ni, procesi so popolnoma optimizirani in digitalizirani.
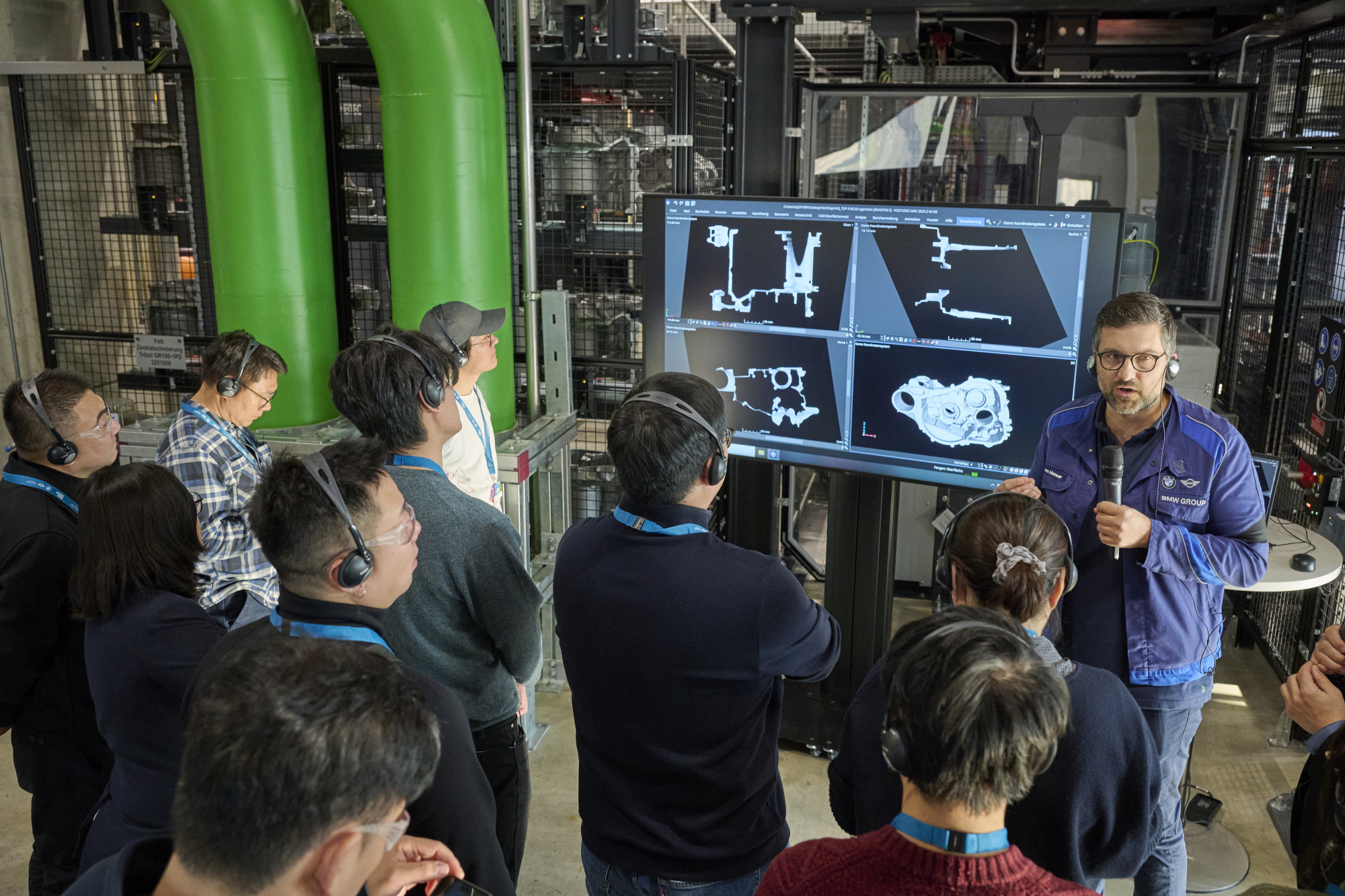
Rentgen si za vsak ulitek vzame 24 sekund, v katerih naredi 2.400 slik. Iz teh nato sestavi digitalno tridimenzionalno skico, s katero prevejajo odstopanja. Skice proučujejo oči in možgani umetne inteligence. Ohranijo jih za morebitno analiziranje v primeru težav. V zadnjem koraku je na vrsti še končni pregled. Tega opravi človek. Robotska roka drži ulitek in ga obrača ter kaže tehniku. Ta po potrebi zbrusi še manjše izbokline. Ohišje elektromotorja, ki ga vgrajujejo v električne BMW-je in prihajajoče modele neue klasse, je tako zaključeno in pripravljeno na vgradnjo.
Tom Kirkpatrick
Dve tretjini uporabljenega aluminija recikliranega
Proizvodnja v livarni me je prevzela. Avtomobil na cesti je nekaj povsem samoumevnega. Za vso prestižno pločevino pa se skrivajo marsikatera izjemna rešitev, inovativen proces ter nizkoogljična proizvodnja. Ob ogledu procesov pa je najbolj očitno, kako ključna je v celotnem procesu varčnost. Energija v Evropi je zelo draga, tovarne v zahodnoevropskih državah pa privilegij najbolj naprednih in dobičkonosnih podjetij. Livarna v Landshutu je edina, ki jo ima skupina BMW v Evropi. Lani so vanjo vložili dodatnih 200 milijonov evrov, od leta 2020 pa skupno milijardo evrov. Razteza se na 87 tisoč kvadratnih metrih. Na leto izdela 3,1 milijona oziroma 71 tisoč ton delov in zaposluje 1.650 ljudi.
Gre za eno najsodobnejših livarn na svetu, zaradi inovativnih in trajnostnih proizvodnih procesov pa je prejela številne nagrade. Od leta 2021 uporabljajo aluminij, za proizvodnjo katerega se uporablja električna energija iz sončnih elektrarn. Ker je proizvodnja aluminija energetsko intenzivna, ponuja uporaba sončne energije velik potencial za zmanjšanje izpustov, pravijo v BMW. Ob jeklu aluminij po masi zajema največji delež materialov, uporabljenih v vozilih skupine BMW. Približno dve tretjini aluminija, uporabljenega v Landshutu, je recikliranega, od tega ga skoraj dve tretjini reciklirajo sami v livarni, še dodajajo.
BMW
Poglej Galerijo
Tom Kirkpatrick
Poglej Galerijo
Tom Kirkpatrick
Poglej Galerijo
Tom Kirkpatrick
Poglej Galerijo
Tom Kirkpatrick
Poglej Galerijo
Tom Kirkpatrick
Poglej Galerijo
Tom Kirkpatrick
Poglej Galerijo
Tom Kirkpatrick
Poglej Galerijo
Tom Kirkpatrick
Poglej Galerijo
Tom Kirkpatrick
Poglej Galerijo
Tom Kirkpatrick
Poglej Galerijo
Tom Kirkpatrick
Poglej Galerijo
Tom Kirkpatrick
Poglej Galerijo
Tom Kirkpatrick
Poglej Galerijo
Tom Kirkpatrick
Poglej Galerijo
Tom Kirkpatrick
Poglej Galerijo
Tom Kirkpatrick
Poglej Galerijo
Tom Kirkpatrick
Poglej Galerijo
Tom Kirkpatrick
Poglej Galerijo
Tom Kirkpatrick
Poglej Galerijo
Tom Kirkpatrick
Poglej Galerijo
Tom Kirkpatrick
Poglej Galerijo
Tom Kirkpatrick
Poglej Galerijo
Tom Kirkpatrick
Poglej Galerijo
Tom Kirkpatrick
Poglej Galerijo
Tom Kirkpatrick
Poglej Galerijo
Tom Kirkpatrick
Poglej Galerijo
Tovarna je v 2023 na medletni ravni zmanjšala porabo energije za približno deset odstotkov. To jim je uspelo z optimizacijo in naložbami v energetsko učinkovitejše tehnologije. Poleg prihranka energije so bistveno zmanjšali tudi porabo vode. Livarna zajema skoraj tri četrtine porabe energije v primerjavi z drugimi tehnologijami. V 2023 so na tem oddelku bistveno zmanjšali porabo zemeljskega plina in s tem izpuste. Optimizacija procesov je omogočila znižanje temperatur taljenja aluminija z 830 na 810 stopinj. Posledica so znatni prihranki energije, kar dodatno izboljša okoljski odtis elektrarne.
Trenutno ni komentarjev za novico. Bodi prvi, ki bo komentiral ...